Yes, the miller syncrowave 250 machines may fail to function as usual. For instance, the device may fail to turn on, the spool gun may fail to work, especially if you place it incorrectly. In such a situation, it is essential to fix the issue immediately before it becomes worse. But sometimes, the problem may persist, especially for beginners or those with little knowledge of using the machine.
Despite the welding machine having some issues, it is possible to fix them without any challenge. First, inspect the whole machine and identify the likely cause of the issue. Try fixing the issue depending on the cause of the case. Finally, seek help if the problem persists.
Fortunately, the article describes the common cause of the issue and the troubleshooting tips. Also, it states the FAQs concerning the welding machine. It is advisable to fix the problems immediately before it malfunctions the whole device.
Contents
Miller syncrowave 250 issues and the troubleshooting tips
a) The immersion is too much or too little
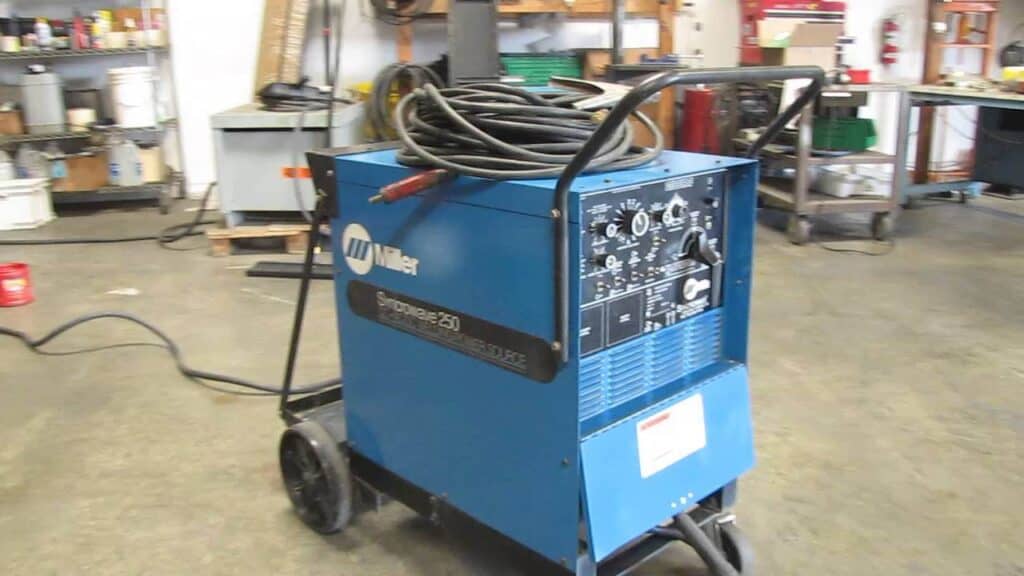
Issue 1: Heat stress makes the soldering metal dissolve via the surface of the metal, which is a risk. The possible troubleshooting tip is to reduce the output voltages range as well as the wire feed rate. You can also help speed the journey.
Issue 2: Inadequate Heat Input: Inadequate heat input, incorrect joint setup, or surface texture thickness. You can fix the issue by first modifying the wire feed rate and voltage to higher levels as a solution. Reduced travel velocity is also a viable option.
Issue 3: Heat stress: Heat stress input that is either too much or too little can cause the weld metal to disintegrate through the surface of the metal, which is dangerous. First, lower the wire cutting speed as well as the output voltages. You can also aid in the hastening of the journey.
Issue 4: Insufficient Heat Input: Insufficient heat input, poor joint configuration, or thick surface texture. As a remedy, increase the wire flowrate and power to higher levels. Traveling at a slower speed is also a choice.
b) Weld Texture Issues
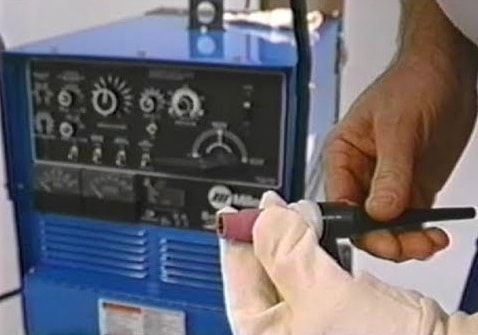
Process 1: Verify that the soldering procedure is correct, including power and welding rod control.
- Use the right soldering procedure for the welding rod.
- Avoid using high welding current.
- At any time, maintain a consistent weave or velocity of motion.
Process 2: Examine the features of the welding rod present.
Use a welding rod that suits the nature of the welder, the base material, and the location of the workpiece.
Process 3: Verify that the welding rod has a design for the welding area.
Do not use a flat position welding rod to perform fillet repairs if you fail to position the pieces.
Process 4: Verify that the joint has been properly prepared.
Make sure that all of the joints are appropriately prepared.
c) low level heat necessary
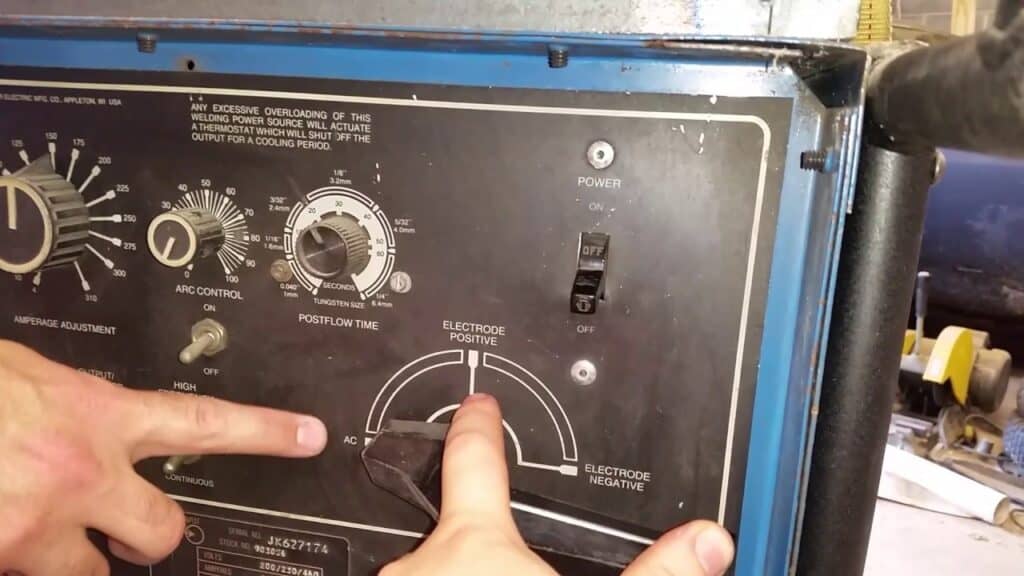
To show that maximum heat sets are insufficient, implying that the weld cannot reach the metal surface due to a lack of heat, use a convex bead.
Solution: Make sure to use the right current for the welding rod present. On the MIG welding equipment, there is normally a table with recommendations. Test the amperage as well if this fails to solve the issue. Excessive splatter will also result from very low power. On the other side, a very high-voltage power configuration challenges the welder to regulate its functioning leading to an undercut.
Issue 2: Incorrect Approach.
Cause: Applying a forehand method, shape the bead flatter.
Solution: A press inclination of 5 to 10 ° is the best strategy.
Problem 3: Work Cable
Cause: Insufficient power in the welding arc due to using the wrong size or defective work cable. The answer is to replace the wires with newer models of the proper size and length that suit the welding machine.
d) Wire feed issues and troubleshooting
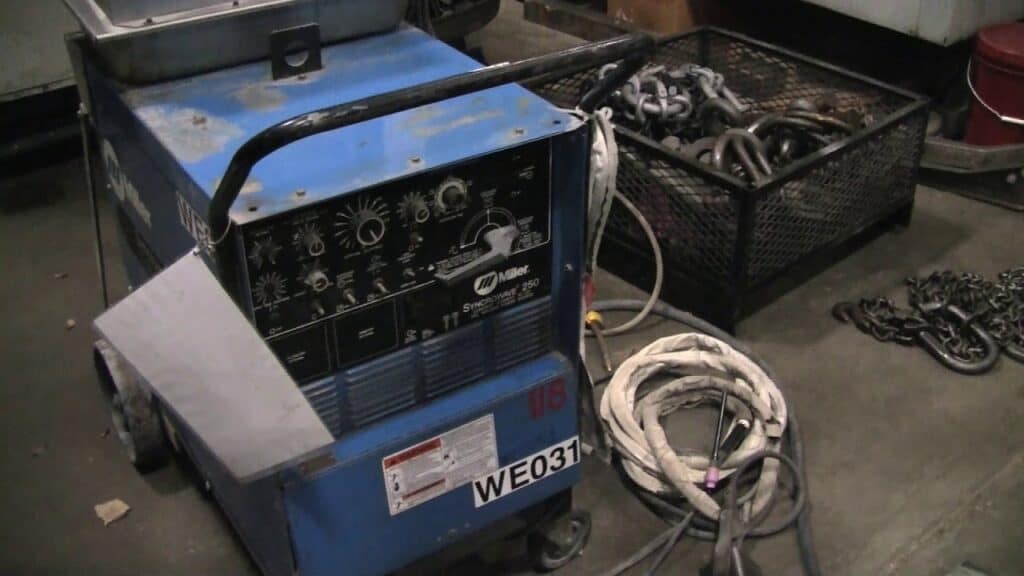
Wire feeding errors can disrupt the welding arc, resulting in a weaker weld bead. The majority of the issues are caused by setting the tool incorrectly.
Problem 1: Bird nesting
Bird nesting is an issue resulting from tangled wires, and the cables damage the wire feed.
Solution: Take the wire out of the pistol by flipping up the drive roll. Re-thread the coiled wire to the gun after trimming it. Examine the tension as well to ensure it isn’t too excessive. Other options include using a bigger thickness cable and spacing the wire feeds closer together.
Problem 2: Burn back
Wire scorching and merging with the friction surface can be caused by utilizing a poor wire inserting rate or positioning the welding machine gun near the bottom material.
Solution: Replace the defective contact tips first, then raise the wire feed speed while keeping the space between the gun and the workpiece at a safe level.
Problem 3: Liner is a problem
The welding machine liner clogging, the use of a liner that is in incorrect size, or badly cut machine liners are all possibilities.
Solution: The wire fed through the cannon liner must be suitably proportioned. Clean or change the liner if there is a clog. Also, follow the recommended guidelines for trimming the welding machine’s liner.
Challenge 4: An old or faulty Gun
If you wire a welding gun incorrectly, an issue occurs. As a result, incorrect wire delivery happens.
Quick fix: If you see a hot spot on the gun while it’s being used, it’s a sign of internal damage. To avoid GMAW welding faults, change the gun right away.
e) Welding Spatter
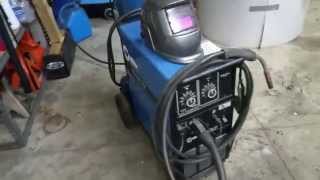
The liquid steel might be ejected from the weld puddle, leaving spatter along with the bead. It has an impact on the look of the weld as well as the fusion intensity. Increased wire feed rate and power adjustments may be the culprit. Other factors include inadequate gas usage and soiled foundation materials.
Reduce the wire feed and current setups and use a smaller welding rod extension as a remedy. Make sure the core material is clean and that the gas is well covered. It’s also crucial to utilize the right injectors and the tips, to prevent an occurrence of an unpredictable arc and also spatter.
Frequently asked questions:
- What are the conditions that result in my miller syncrowave 250 problems?
The following are some of the most common conditions of problems:
i. Use of reduced shielding gas with high humidity. High humidity can also be a source of issues.
ii. Tools that aren’t up to snuff
iii. Contaminated metals and filler rods
iv. Shielding airflow is irregular.
v. Welding adjustments
vi. Pollution on the ground
vii. Concerns about gas supply that is Inadequate gas flow contaminates electrodes and parts.
viii. Thermal protection issues
ix. Current fluctuations caused by the usage of other workplace machines or improper power
x. Because of a mismatch between the nozzle and the welding rod, the nozzle overheats.
Conclusion
If you have issues with your miller syncrowave 250, check the welding gun if it is in a good position. If not, change the position and insert it properly. Tighten it if loose. Also, read the article above and identify the common problems with the troubleshooting steps or tips.
Finally, after checking all the parts, consider seeking help from a professional, but the issue persists. Also, consider replacing the whole machine if it is faulty beyond repair. When using the welding machine, it is essential to take precautions, such as following the manufacturer’s maintenance schedule.