A variety of factors can cause welding issues. They are frequently the result of poor method or parameter selection, such as inadequate shielding gas coverage or inappropriate travel rates. Welds that aren’t up to par aren’t worth having. A weld is intended to combine two metal components by utilizing a similar metal as a filler material. A faulty weld is unattractive and risky, especially in construction sites, where people’s lives may be at risk.
The most successful welding procedure depends on the material’s shape and thickness. The most prevalent types of welding nowadays are MIG (Metal Inert Gas), Flux-Cored Arc Welding (FCAW), GMAW (Gas Metal Arc Welding), and SMAW (Shielded Metal Arc Welding). Superior welding equipment has simplified these processes over time. With such equipment, many welders overlook essential measures. However, when these same welders have problems, they are unable to identify and fix them.
In this article, we will go through various frequent welding faults and how to fix them. Find also the best answers to the frequently asked questions on fixing a bad weld. Let’s start;
Contents
Common welding defects and how to fix them
They include;
1. Spatter
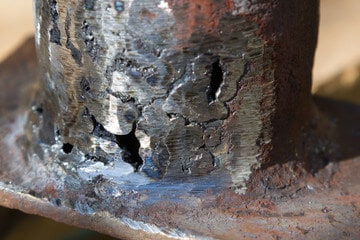
A common unintended side effect of GMAW (Gas metal arc welding) is the formation of spatter. These are usually droplets of a molten material created near the welding arc. Spatter occurs when the welding speeds are too high, polarity is incorrect, or gas shielding is inadequate. To avoid spatter, it is recommendable that the welding current and arc dimensions be reduced.
Additionally, the welder can verify that the consumable is being used with the proper polarity. Finally, it is essential to check the type of shielding and flow rate, clean the nozzles, and increase the angle of the torch to the plate.
2. Porosity
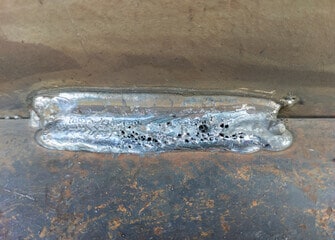
Porosity is created when nitrogen, oxygen, and hydrogen are absorbed in the molten pool and subsequently expelled during solidification, becoming confined in the weld. Porosity can be caused by various factors, including rust, grease, or painting on the plate boundary, presence of moisture, inadequate gas shielding, or even when welding is performed on small gaps with air trapped between them.
Welders need to re-bake or use new welding consumables to eliminate porosity in their welds, and they should also inspect their particular welding torch for defects. It also helps if the plate borders are dry and clean. Also, it would be an excellent approach before welding to evaluate the gas and flow rates, clean the equipment nozzles as well as ensuring a proper angle is maintained between the torch and the plate.
3. Inclusions of Slag
Slag inclusions are microscopic flux particles that become lodged in the weld metal, preventing the weld from fully penetrating. To avoid this, ensure that flux-coated consumables are kept in good condition. It would be essential to have the correct current, voltage, and arc parameters to achieve quality welds with full fusions while running through.
4. Deformation
When welded metals compress during the cooling and hardening process, deformation occurs. This occurs when the welding process is incompatible with the desired weld, there are numerous tiny beads, or improper plate fit-ups before welding. Avoiding deformation can be accomplished by welding from both joint ends, welding in opposite directions (from the center out), using a bigger electrode, and gripping tightly. Changing the order of welds, the position of the joint, or the number of passes can all assist in mitigating the risk.
5. Undercut
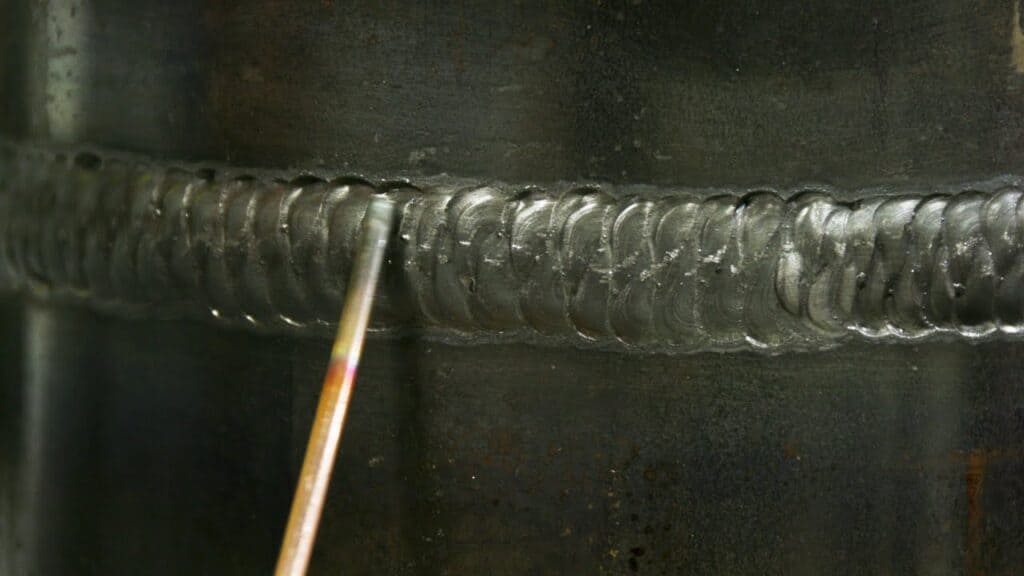
Undercuts appear when the voltage of the arc is excessively high, or the arc is lengthy. Using the electrode incorrectly, angling it wrong, or making it too large for the plate thickness can all cause undercuts. Additionally, undercuts are more likely to happen when the flow rate is too fast. Apart from monitoring the speed, it is critical to ensure that the electrode is being appropriately handled.
I recommend that welders should not use a larger electrode than necessary because if the volume of molten material becomes excess, an undercut will occur. Following that, it’s critical to monitor the amount of weave used. Lastly, avoid holding the electrode too close to the vertical plate when welding a horizontal fillet weld.
6. Cracks
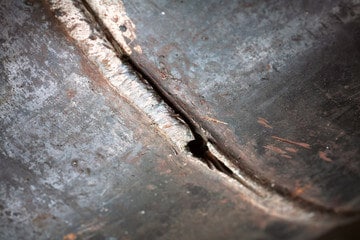
Every fracture (regardless of its size) is regarded as a fault in any construction. Small cracks tend to grow bigger over time, which can be harmful. It is not as just filling in the gaps with materials as fractures should always be smoothed and a new weld produced to correct the mistake. Due to the tedious nature of this procedure, prevention is preferable to cure.
To avoid cracks, the plates’ edges should be ground, scraped, filed, or deburred to ensure that they fit together easily. Try to reheat both sides of the joint, as proper temperature control is critical, and then clamp the plates together. Also, before you begin welding, verify that you have the appropriate temperature dialed in by testing the equipment settings.
7. Partial penetration and fusion
Incomplete root fusion occurs when one side of the root joint does not fuse properly. When the root area of the joint is unfused on both sides, partial root penetration occurs. These difficulties are especially prevalent in consumable electrode processes. As the electrode wire or rod is consumed by the arc, the weld is deposited ‘automatically.’ There are numerous possible solutions, including using a larger root gap and electrodes with a diameter equal to or greater than the root gap width. When welding, it is recommended to reduce the travel rate and weave in between plate boundaries.
8. Incorrect delivery of wires
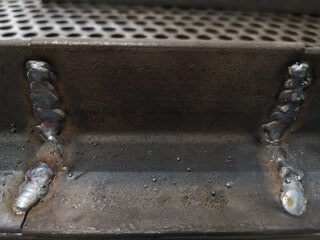
The wire distribution system may be problematic when welders begin to experience chattering sounds within the gun cord. This is always the case in this circumstance, as it pertains to the proper configuration and maintenance of the equipment. Occasionally, welders make the error of adopting too broad tips for the application, which might result in some of the additional welding issues noted above.
Several tips include double-checking the contact tip of your gun and the wire size that you will use. It is prudent to inspect the wire’s end to see whether it is worn out and requires replacement. Regarding the drive rolls, they should be checked over time since they do wear out. Always maintain proximity between the drive rollers and the guiding tube.
Frequently asked questions:
- Can a weld be rewelded multiple times?
Answer; Re-welds in low alloy steels are regulated by the heat-treated conditions that they were supplied. For Cr-Mo steel products, up to two rewelds are possible; however, care should be given to post-weld heat treatment activities and the possible degrading of the welded joint as a result.
- How do you determine the difference between a good and a bad weld?
Answer; A good weld will exhibit a homogeneous bead free of pores or granules of melted metal. A low-quality weld will have gaps and be inconsistent in appearance. Additionally, you’ll discover inadequate penetration of workpiece materials. Further, big globs of molten metal may be present on and surrounding the weld.
Conclusion
The reasons for bad welds are numerous. However, by following proper welding practices and employing high-quality equipment, most welding difficulties can be avoided entirely. This article has outlined the various welding problems and their corresponding fixing tips.
Having the appropriate information on eliminating welding mistakes and getting the best welding equipment with the most up-to-date innovation will make a difference in reducing the likelihood of faults occurring. Thus, having dependable suppliers renowned for product excellence is critical for organizations that rely on welding as a crucial component of their fundamental company structure.