A miller cst is sophisticated and complex equipment. when one minor thing is not good, it significantly impacts the welding equipment and the welding job. The welding equipment may not perform properly or even start if something is wrong.
It is not always essential to replace the entire unit; the user can identify and resolve some issues or obtain assistance from a more experienced person. However, knowledge on basic fixation methods is quite beneficial to you, as it saves them time and money spent on repair shops.
Here are some of the most common issues that a miller cst 280 confronts. Then, again, we will look at the ways to troubleshoot the problems for better working of the miller.
Contents
The miller cst 280 problems
First and foremost, it’s critical to understand numerous problems that a miller cst 280 may suffer; this allows one to inspect and repair the unit’s many components.
1. The miller cst 280 will not start
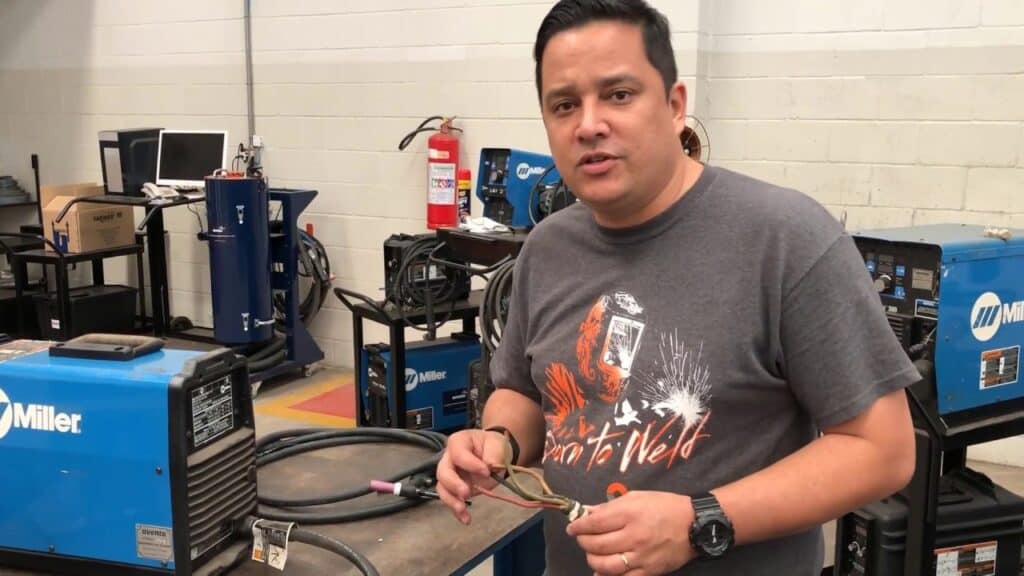
The welding machine will occasionally not start. It could be caused by a blown fuse from the power supply line, a power circuit that isn’t working, overload, or incorrect input of voltage.
Solution: If the miller cst 280 will not start, then ensure that the machine’s switch is turned on, and then thoroughly investigate the reason for the issue. If it’s a blown fuse, ensure that you replace it. If the circuit is the issue, it is necessary to verify and fix the input voltage. If the cause is overloading, it is better to leave the miller cst 280 to cool down for a while. Then, the voltage input is checked twice, and the input should match the manual’s specifications.
2. The miller cst 280 welding machine’s starting works, but the fuse blows
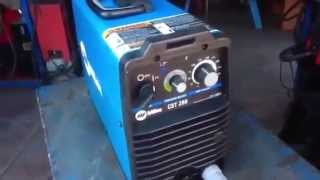
Cause: The welding equipment will sometimes start up and be ready to work, but the fuse will blow. The cause could be either the fuse is too small or In the connectors, there is a short circuit.
The solution is to figure out what’s causing the issue in the first place. If a blown fuse is the cause, the fuse size must be replaced and expanded; if a short circuit is the cause, the connections must be reviewed, and the leads must be insulated.
3. The welding machine abruptly comes to a halt
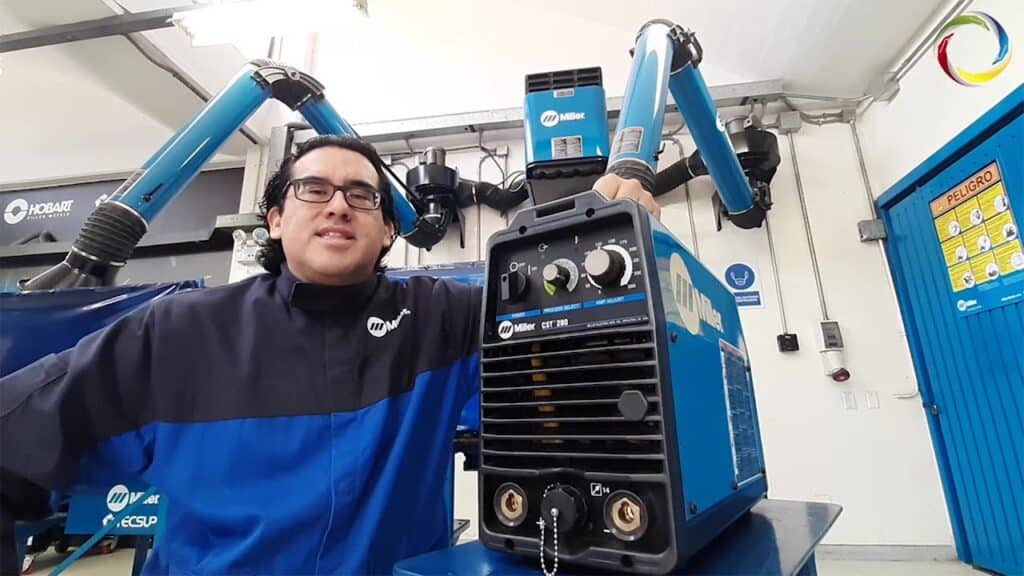
Cause: During welding, the welding equipment frequently stops suddenly. This issue could be caused by a blockage in the ventilation system, a malfunctioning internal cooling fan, or overloaded.
Solution: Check to see that all of the ventilation cases are free and clean. If they are dirty, they are cleaned so that ventilation is not obstructed. Before the internal cooling fan may resume operation, the connections and main lead must be fixed or upgraded. Never overwork the equipment, and only work according to the specified duty cycle.
4. A faulty polarity switch
While the welder is still operating, the polarity switch will occasionally stop working due to a worn connection or lack of using the switch correctly. Solution: Never be using the polarity switch while the welder is in use, since this may cause the polarity switch to malfunction. The switch is replaced if it has become worn out.
5. The holder for the electrodes heats up
In many circumstances, the electrode holder heats up. The cause of this could be a loose connection or an electrode holder with an insufficient duty cycle.
6. When you contact the welder, you get electric shocks
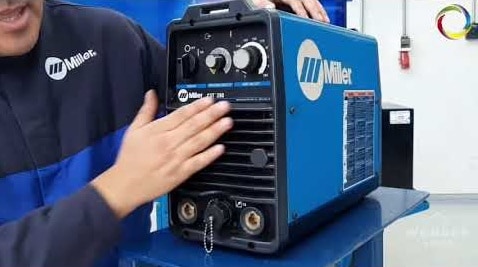
Cause: While touching the welder, the user may experience tiny electrical shocks. That is not always the case, but it can be harmful. This problem develops when the welding machine’s frame is not correctly grounded.
To solve this problem, read the user handbook thoroughly and learn how to ground the welding machine’s frame and ground the cover properly so that the user does not experience shocks when touching the welder.
The welding cable is heated.
The welding cable might become extremely hot at times. It happens when the welding machine’s cable isn’t the right size or has an insufficient duty cycle.
Solution: As directed in the user manual, the cable is changed to the proper size. In a welding machine, a cable with the proper duty cycle size is critical.
7. A faulty ground clamp
Cause: The welding machine’s ground clamp may become coated with oxides, causing the clamp to deteriorate. As a result, electrons cannot easily transfer, resulting in high resistance on the machine, affecting current flow.
Solution: The ground clamp should be examined and cleaned regularly to avoid any oxide build-up and extra welding machine resistance.
8. cable that has been damaged
The cable may be damaged and have frayed and worn parts after a lengthy period of use.
Solution: Replace the welding machine’s cable as quickly as possible, as a damaged cable can cause a slew of difficulties for the machine, as well as a significant impact on the welding process. It is vital to inspect the wires for any signs of damage from time to time.
9. The welding equipment does not turn off
Cause: It is possible that the machine will not turn off even if the switch is pressed until the power supply is disconnected. When the line switch is worn out or fails mechanically, this happens.
Solution: If the welder’s line switch is damaged, the switch and connection must be repaired or replaced.
10. Welding flaws
Aside from welding machine issues, some welding flaws occur frequently, which the user can easily correct by adjusting and repairing key sections of the welding machine. Here are some of the welding flaws you might come across:
11. Poor wire feeding Cause
A worn-out driving roller could be the cause of improper wire feeding. When a driving roller is worn out, the wire feed is affected and may slip.
Solution: If this problem occurs, examine the welding machine’s liner for any dirt or debris. The machine is thoroughly cleaned to get the drive roller to work properly again with adequate wire feeding.
12. Low welding cause
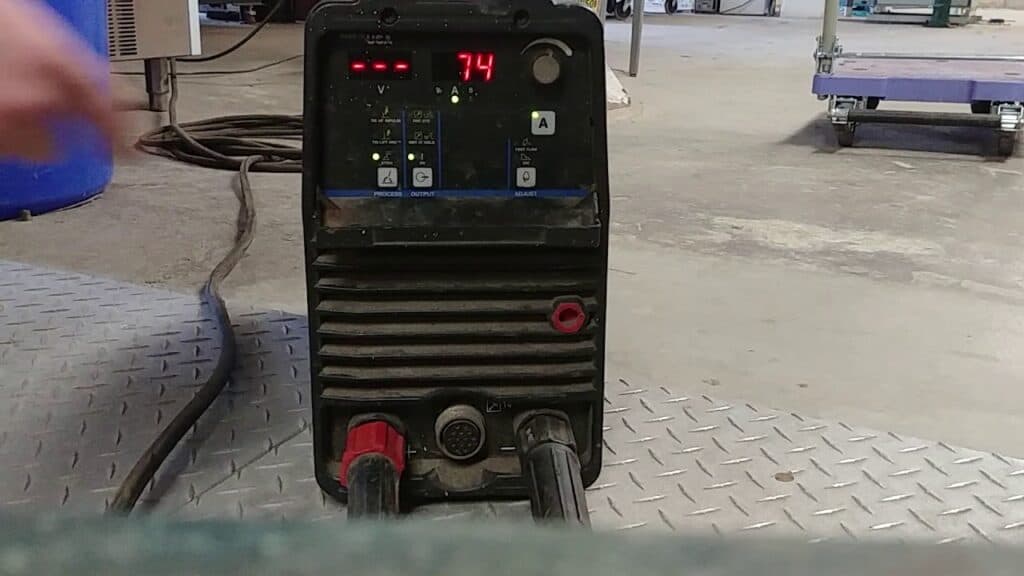
When the tip within the welding gun wears out, the power supplied by the welding machine is insufficiently applied, resulting in additional work for the welder because the welding isn’t completed effectively.
Solution: If this problem occurs, change the tip inside the welding gun as soon as possible, as this may cause additional issues such as a poor wire. The tip is changed right away to avoid more problems.
13. There’s a lot of spatter
Excessive spatter can occur on the weld most of the time, caused by too much high voltage, too much CO2, or improper impedance.
Solution: To minimize excessive spatter, the welding machine’s voltage should be regulated, and a suitable voltage applied. To reduce spatter, a gas heater is utilized to heat the CO2.
Conclusion
In addition to all of the tactics for maintaining and repairing, the miller cst 280 welding equipment maintenance is critical. Keep the following in mind at all times.
- It is necessary to keep the welding machine clean. It is necessary to clean the various elements of the machine regularly.
- Check for any damage to the machine’s parts from time to time. Even the tiniest tear or wear is carefully examined.
- According to the instructions, the cables and other supplementary equipment used with the welding machine must have the proper duty cycle size and be compatible with the machine.
- Never overburden the machine and never go beyond the welding depth limit.
- The welding machine must be kept cold and dry at all times.
Though the welding machine is a complex instrument, it will last a long time and consistently deliver the necessary results if it is properly maintained.