Millermatic 211 wire feed problems cause the MIG wire to fail to feed the welding machine enough resources to make the metals. The problems with the wire feed can cause many issues with the welding machine that will cause an increase of costs of some resources the welder needs to weld the metals properly. The problems can also lead to pressure on an individual who keeps thinking about what to do for the wire and can cause the production of poor products for the industry.
The millermatic 211 wire feed problems can occur at any place on the welding machine, more so on the gun that is the main part of welding metals like aluminum and other areas. Therefore, before concluding that the machine’s wire has a feeding problem, it is good to check the whole system and diagnose the problem with it. There are a few things you can also do to check the wire feed problems with your machine.
So you want to know what to do with the millermatic problems or how to avoid them? Well, we got you covered because here is what you can know what to do. First, the guide will summarize what to do with your wire, including what you can do if you find out that the millermatic 211 has wire feeding problems. Reducing the problems helps reduce the costs for repairing the wires and reduces the production of poor-quality welds. The guide also contains the frequently asked questions and, lastly, the conclusion, which carries the full content of the guide in summary.
Contents
What can you do for the millermatic wire feed problems?
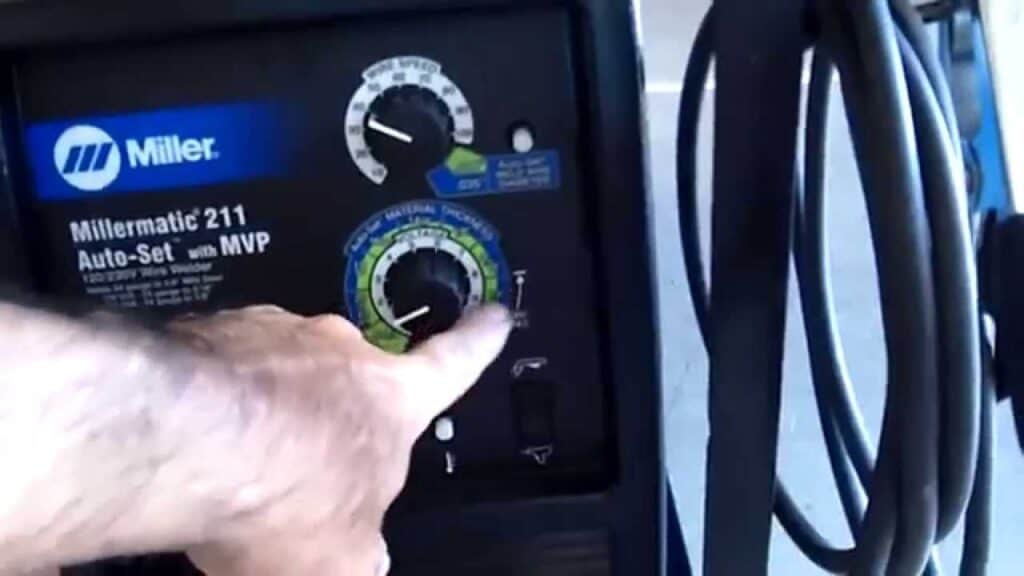
When experiencing the millermatic wire feed problems, consider visiting different areas that cause the wire to have feeding problems. The major area that causes the problems you need to visit is the areas around the wires, which include the hub, the drive roll, inlets, and gun liner. Some other areas are around the gas position, including the regulator, the gun, and the flow area.
1. Survey the nature and quality of the wire with problems
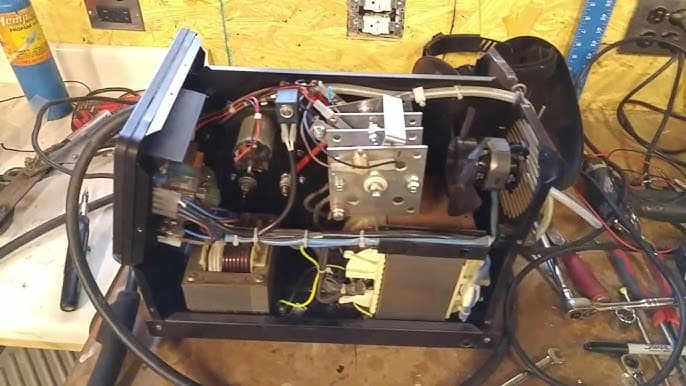
The first thing the welder must do is check the wire feed as a whole with care to identify its issues. Sometimes exposing the wires to any source of moisture can damage the wires since moisture is water that can react with the metal wires to cause rust that makes the wire fail to perform correctly. After checking the wire and finding out that it has rust, consider removing it and fixing a clean wire to work. The welder can also blow out or fix the liner on the wire after replacing the wire. The wires need maintenance practices that help keep them for long such that the user needs to keep the wires in a particular bag or in any safe place that cannot allow moisture to penetrate that will help keep the wire and save you from any other additional costs.
2. Fine-tune spool and drive roller forces
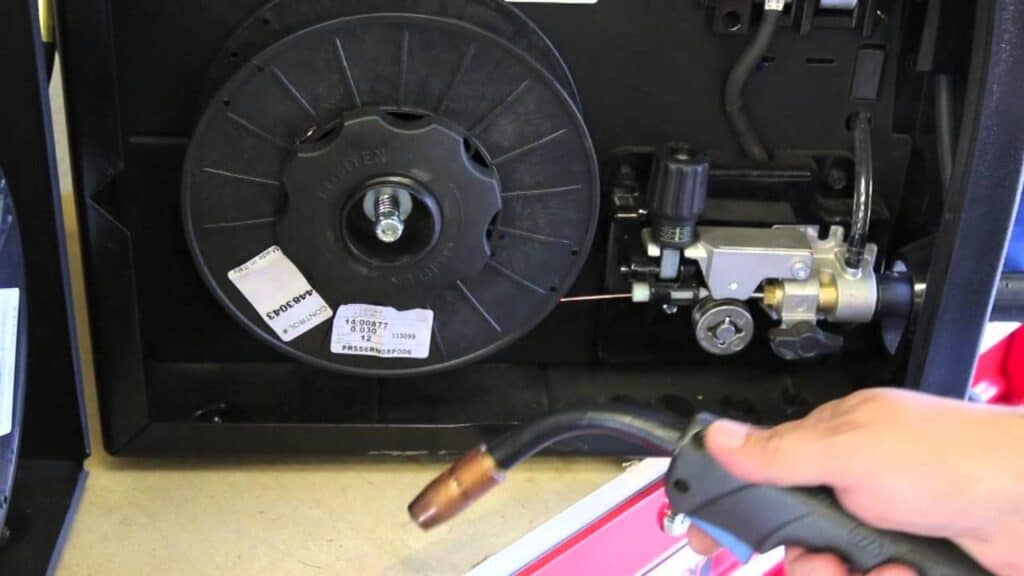
The wire feeding problems can result from the spool, which faces poor force on their spool breaks, drive rolls, or in any parts around them. The poor force can either be excess or less. The excess force causes the wire to wear and tear, which can later cause bird nesting on the wire; therefore, it is good to check the spool and the rollers in the machine. There are steps that you can follow when checking the areas in the spool and the rollers, which are as follows:
i. Ensure you make the drive rolls loose and then increase the force while feeding the wire into a welding material. Repeat the same process when increasing the force until you overpass the wire slippage.
ii. If the drive rollers are getting tighter with the tension than the way they were before, inspect the wear and tear with the wires. And if the wires are okay, you can adjust the settings with the spool to ensure they are correct and that the wire is in the right position. If everything is okay, consider checking the drive rolls with some other issues. For example, ensure the drive rolls are of the correct type and size for the machine.
3. Check the gun liner
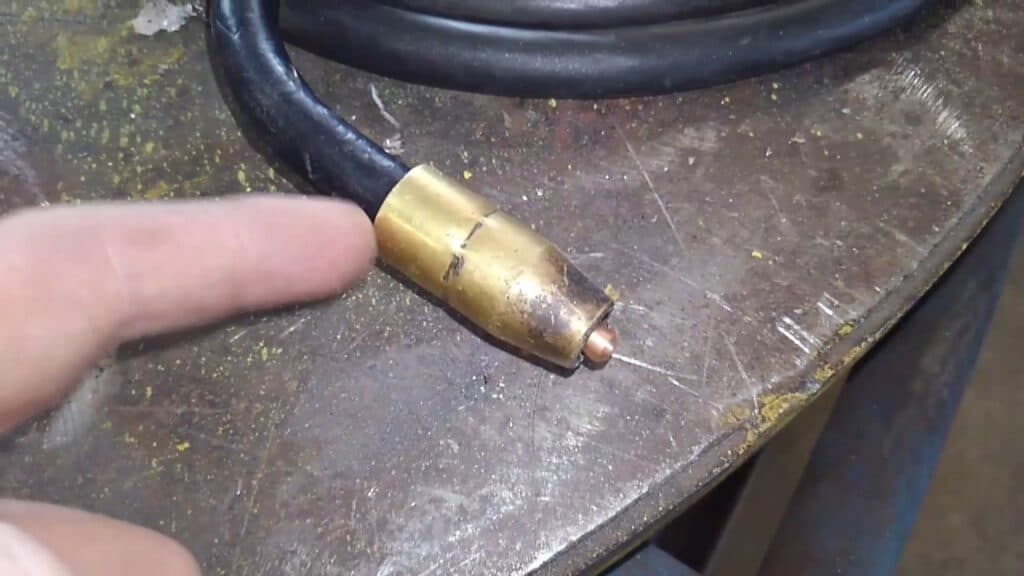
Gun liner enhances the welding process because of its length in the machine since any gun liner that works with the wire has some faults like some can be dirty, or that dust accumulates in them can cause the wire to have poor feeding problems. If the gun liner has some issues consider replacing it because changing the liner is cheap, that it will cost less. However, despite being cheap, it can take a lot of time to change the gun liner.
But if the problem with the gun liner is because of the dirty objects accumulating in it, consider removing the dirty particles by blowing them out with some pressure of compressed air. It is good to ensure the gun liner is the right one for the machine; the liner is of good quality and maintains its size in the whole welding process. The maintenance practices help in prolonging the life span of the machine and reduce the wire feed problems.
4. Contact tip
The last thing to consider is the contact tip, where the contact tip has an ID that must match the size of the wire feeding the machine, and the contact tip hole is round in shape to fit the wire well. If the hole is not round, it means it experiences wear and tear and can cause wire-feeding wire problems. Moreover, it is good to check the stick to help it maintain its normal position since a long or short stick causes the contact tip to turn back, which makes it have wire feeding problems.
You might be interested to read our another comprehensive article of: How To Troubleshoot Miller Syncrowave 250
Frequently asked question:
- What are the signs and symptoms of a wire feed problem?
There are several signs of a wire feed problem in the millermatic 211 machines. The signs include: bird nests, some wires fail to pass through the torch, the drive roll slips on the wire, the arc length keeps changing, there is a burn pack on the contact tip, and sometimes the wire feed rate becomes slow.
- What are the solutions to the signs of the wire feed problems?
Check the features of the wire when it starts to work slowly, check the force the spool applies, inspect the drive rollers and their forces, and ensure the size of the contact tip matches the wire correctly to avoid feeding problems.
Conclusion
Now you have the full information of the millermatic 211 wire feed problems where they have their solutions since the causes are within some parts of the machine. In addition, the guide contains the actions the user must do to reduce the causes of the wire feeding problems in the machine. Reducing the problems helps reduce the costs of purchasing new wires for replacements every time. In addition, it increases the rate of welding the machine and helps produce quality welds in the industry.
Therefore follow the guide carefully to check the parts that cause the wire feed problems in the machine. Remembering the machine against some problems helps save the lifespan of the machine so that you can use it for a long time without any errors and if it is for business, it can lead to good profit to the user if you do not have some more things for the machine to work.