Yes, the welding rod size for metal thickness is essential in carrying out the welding process. Welding is one of the processes you use to melt metal, such as steel or aluminum. The process involves the use of high heat and pressure to join two different or same metals together. Different welders apply other techniques to join metals together to create the best and desired products. Most people prefer using two common welding methods. The methods include; MIG and TIG welding.
The welding methods depend on the thickness of the metal. For instance, the welding techniques include; friction welding, laser welding, among others. Each method has its benefits and cons. For example, the MIG method uses only thick metals, while the TIG welding method is much faster and cheaper than the MIG. Therefore, it is essential to consider the thickness of the metal rod before beginning the welding process.
The article below summarizes the welding rod size for metal thickness essential for the welding process. Also, it shows different or categories of the welding rods present in the market today. Finally, it shows the FAQs concerning the welding rod size for metal thickness.
Contents
The common welding rod size for metal thickness
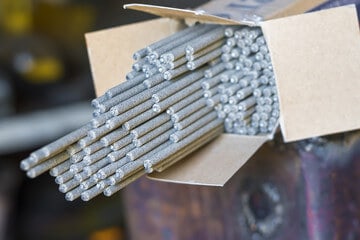
Welding rod is mostly used to refer to the best electrode a welder can use to join metals together successfully. Electrodes are either consumable or non-consumable, and it is essential to choose an electrode that suits your choice. Electrodes contain different numbers.
The first two numbers on the electrode indicate the strength of the electrode. For instance, an electrode with a 70 number indication signifies that the electrode has a potency of approximately 70,000 pounds in each square inch. Also, the welding rod has another number, a third that indicates where you can apply the electrode. For example, electrodes with number 1 show you can use the electrode in all positions, 4 indicates overhead and horizontal positions. In contrast, number 2 shows you can use the electrode only in either horizontal or flat directions.
The last numbers show the insulating on the electrode and the amount of power you can use with the electrode. Therefore, it is essential to understand all the numbers present in the welding rod you are using during the welding process.
Different common welding rod sizes
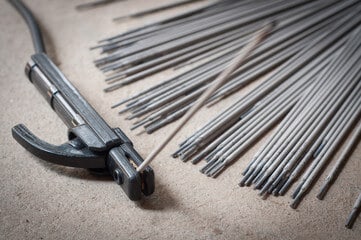
Electrodes exist in many different sizes. Also, the electrodes have different diameters and thicknesses. Therefore, it is essential to consider the level of thickness of the welding rod before purchasing it or beginning the welding process. Electrodes come in different models, including 7024, 6010, 6011, 7018, among others.Shortcode
Electrode inches in diameter | Electrode type | Metal thickness |
1/16 inches | 20-40 | |
5/64 inches | 25-60 | |
Ranging from 3 to 16Ranging 3/32 inches | 35-145 | Ranging to ¼ |
1/8 inches | 75-190 | Ranging to 1/8 |
5/32 inches | 110-250 | It is above ¼ |
3/16 inches | 140-305 | Above 3/8 |
7/32 inches | 170-365 | |
¼ inches | 210-430 | Above 3/8 |
5/16 inches | 275-525 | Above 1/2 |
If the welding rod is thicker, the current necessary for the welding process is higher, and the electrode is usually larger due to its thickness. The welding thickness depends on the type of electrode. The information below describes the common electrode sizes present and their classification.
1. 7024 electrodes
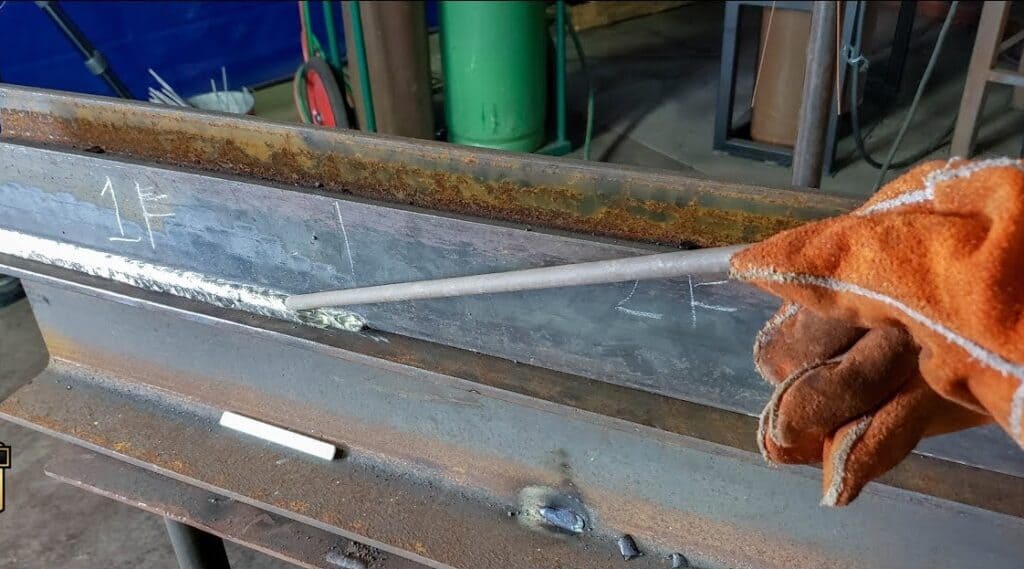
The 7024 electrodes require high current, thus raising their rate of deposition. The recommended position to apply them is either on a flat surface, horizontal and their puddle is usually large and very hot with a flux that is essential in regulating the solidarity of the metal. In terms of sizes, they perform best in a quarter inches’ metal thickness, and you can use them in half-thick metals. They require more current when compared to other electrodes of different models.
You don’t need a rod oven when using them since you can lay them flat on the surface or horizontally during the welding process. Further, they are beneficial in that they are easy to clean since they emit a slag that one can remove easily. When it comes to price, they are cheap. Despite having many advantages, the electrodes have some cons, and they include; they require a lot of heat and pressure to melt thicker metals hence very dangerous to the welder.
2. 7018 electrodes
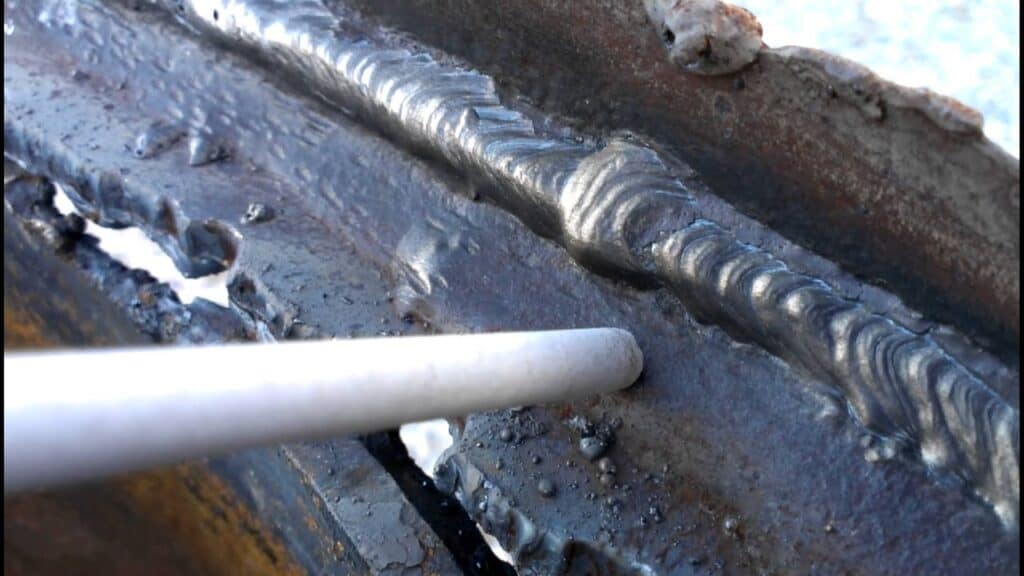
When it comes to easiness, this type of electrode is the most recommended. The 7018 electrodes come with a thicker flux, and they contain a high amount of powder. When using electrodes, they penetrate at a low rate, resulting in the emission of a smooth product that spatters less when compared to other electrodes. You can use the electrode in all positions, such as flat, horizontal, and vertical, without any issues. The thickness of the metal necessary is approximately a quarter, and its strength is around 70,000 pounds.
In terms of current, the electrode requires a high current that is either alternative or direct; AC and DC+. If you want to produce a smooth metal, drag the rod across the surface and change its position, including the side position. Also, the changing process allows the welder to melt a strong metal that is desired.
Despite having many benefits, their low hydrogen content results in special storage to increase their longevity. Poor metal storage may result in the welding process, and they do not withstand water or any moisture. Most people prefer using them in building large bridges, nuclear power plants, and pressure pipes. The most recommended electrode is the Forney 30681 welding rod.
3. 6010 electrodes
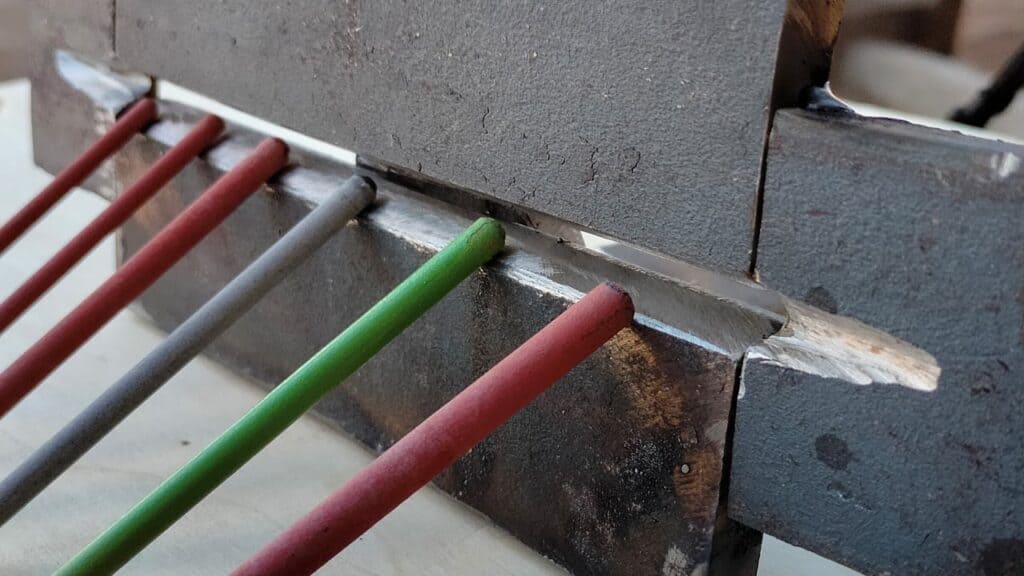
The electrodes require only direct current, and their coating is cellulose coating. When it comes to penetration, the 6010 electrode has deep penetration and can flow through many areas, including dusty areas, rusty places, painted areas, and oily places. The electrode is easier to clean since it functions smoothly without any difficulties. Despite having many pros, the electrode is not as easy to use as other electrodes.
Further, you can use the electrode in dry temperature conditions and can withstand moist places. When using them, you must apply some little moisture and avoid drenching this type of electrode. If you drench the electrode, you may damage it easily or completely and increase the cost of purchasing a new one. The most recommended electrode of this type is the Forney 31610 electrode.
4. 6011 electrodes
The type of electrode requires either direct or alternating current to function effectively. Like other electrodes such as the 6010 electrodes, you can use them in different places, including dusty areas, rusty areas, painted areas, and oily areas. Despite being effective in many areas, it is difficult to clean them if you compare it with other electrodes, even if it emits little slag. Therefore, following the manufacturer’s instructions is essential when cleaning them to obtain the best positive results. The most recommended electrode is Forney 31205
5. 7014 electrode
When compared to 6012 electrodes, both have the same joint penetration. You can use them on carbon metal and very soft alloy metals such as steel. When it comes to current, they require a high amount of current to melt thick metals, and the current rate increases their deposition. Also, they can hold a higher amount of amperage when compared to other electrodes such as 6012. You can use the electrode in places such as farm machinery and automotive parts. The most recommended is the blue demon 7014 electrode.
6. 6012 electrode
These 6012 electrodes are suitable in all directions and require high speed and high current, especially if you use them horizontally. Their penetration is not deep like other electrodes such as 6011 and 6010. The cleaning process after welding is tiresome since the slag is sticky, even if it is small.
Frequently asked questions:
- When can I use an electrode with high deposition?
Sometimes, one can be in a hurry and wish to fish for his job within less time. In such conditions, one must be able to choose an electrode with very high deposition. The deposition must be able to stick very faster to reduce the time spent in joining the metals together. The electrodes with high deposits are most recommended for their excellent dal for non-essential functions when one needs to simply weld metals
If one needs to perform essential welding for a certain organization, it is not advisable to use an electrode with very high deposition. It is not advisable because they cannot withstand applications such as boiler manufacturing and pressure vessels where the only condition recommended for welding is a lot of stress. Melting an iron powder with excess pressure results in extra fluid that will destroy the whole welding process.
Conclusion
When buying the electrode, there are some factors you need to consider. The factors include; tensile strength of the welding rod, the current necessary, and the position in which the welding metal is going to be used. Also, consider polarity and the thickness of the rod. Therefore, choose a welding rod with thickness and size that suits your choice.
Finally, perform some projects to know the best electrode. Also, before purchasing the electrode, seek help concerning the seller and ensure he is selling a genuine product. Also, if you are buying online, the most recommended websites are the Amazon and eBay websites.